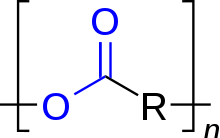
(the ‘ester’ component is shown in blue)
.
-as of [6 FEBRUARY 2025]–
.
.
-[poly-ester] is a ‘category’ of ‘poly-mers’ that contain the ‘ester functional group’ in every ‘repeat unit’ of their [main chain]-
.
As a specific material, it most commonly refers to a type called ‘polyethylene terephthalate’ (PET).
Polyesters include naturally occurring chemicals, such as in the cutin of plant cuticles, as well as synthetics such as polybutyrate.
Natural polyesters and a few synthetic ones are biodegradable, but most synthetic polyesters are not.
The material is used extensively in clothing.
Polyester fibers are sometimes spun together with natural fibers to produce a cloth with blended properties.
Cotton-polyester blends can be strong, wrinkle- and tear-resistant, and reduce shrinking.
Synthetic fibers using polyester have high water, wind and environmental resistance compared to plant-derived fibers.
They are less fire-resistant and can melt when ignited
Liquid crystalline polyesters are among the first industrially used liquid crystal polymers.
They are used for their mechanical properties and heat-resistance.
These traits are also important in their application as an abradable seal in jet engines.[3]
Natural polyesters could have played a significant role in the origins of life
Long heterogeneous polyester chains and membraneless structures are known to easily form in a one-pot reaction without catalyst under simple prebiotic conditions
.
Types
Polyesters are one of the economically most important classes of polymers, driven especially by PET, which is counted among the commodity plastics
in 2000 around 30 million tons were produced worldwide
The variety of structures and properties in the polyester family is very large, depending on the nature of the R group
(see first figure with blue ester group)
.
The family of polyesters comprises
Linear aliphatic high molecular weight polyesters (Mn >10,000) are low-melting (m. p. 40 – 80 °C) semicrystalline polymers and exhibit relatively poor mechanical properties.
Their inherent degradability, resulting from their hydrolytic instability, makes them suitable for applications where a possible environmental impact is a concern, e.g. packaging, disposable items or agricultural mulch films[8] or in biomedical and pharmaceutical applications
Aliphatic linear low-molar-mass (Mn < 10,000) hydroxy-terminated polyesters are used as macromonomers for the production of polyurethanes.
hyperbranched polyesters are used as rheology modifiers in thermoplastics or as crosslinkers in coatings[10] due to their particularly low viscosity, good solubility and high functionality[11]
Aliphatic–aromatic polyesters, including poly(ethylene terephthalate) and poly(butylene terephthalate), are high-melting semicrystalline materials (m. p. 160–280 °C) that and have found use as engineering thermoplastics, fibers and films.
Wholly aromatic linear copolyesters present superior mechanical properties and heat resistance and are used in a number of high-performance applications.
Unsaturated polyesters are produced from multifunctional alcohols and unsaturated dibasic acids and are cross-linked thereafter; they are used as matrices in composite materials. Alkyd resins are made from polyfunctional alcohols and fatty acids and are used widely in the coating and composite industries as they can be cross-linked in the presence of oxygen. Also rubber-like polyesters exist, called thermoplastic polyester elastomers (ester TPEs). Unsaturated polyesters (UPR) are thermosetting resins. They are used in the liquid state as casting materials, in sheet molding compounds, as fiberglass laminating resins and in non-metallic auto-body fillers. They are also used as the thermoset polymer matrix in pre-pregs. Fiberglass-reinforced unsaturated polyesters find wide application in bodies of yachts and as body parts of cars.
Depending on the chemical structure, polyester can be a thermoplastic or thermoset. There are also polyester resins cured by hardeners; however, the most common polyesters are thermoplastics.[12] The OH group is reacted with an Isocyanate functional compound in a 2 component system producing coatings which may optionally be pigmented. Polyesters as thermoplastics may change shape after the application of heat. While combustible at high temperatures, polyesters tend to shrink away from flames and self-extinguish upon ignition. Polyester fibers have high tenacity and E-modulus as well as low water absorption and minimal shrinkage in comparison with other industrial fibers.
Increasing the aromatic parts of polyesters increases their glass transition temperature, melting temperature, thermal stability, chemical stability…
Polyesters can also be telechelic oligomers like the polycaprolactone diol (PCL) and the polyethylene adipate diol (PEA). They are then used as prepolymers.
Aliphatic vs. aromatic polymers[edit]
Thermally stable polymers, which have a high proportion of aromatic structures, are also called high-performance plastics; this application-oriented classification compares such polymers with engineering plastics and commodity plastics. The continuous service temperature of high-performance plastics is generally stated as being higher than 150 °C,[13] whereas engineering plastics (such as polyamide or polycarbonate) are often defined as thermoplastics that retain their properties above 100 °C.[14] Commodity plastics (such as polyethylene or polypropylene) have in this respect even greater limitations, but they are manufactured in great amounts at low cost.
Poly(ester imides) contain an aromatic imide group in the repeat unit, the imide-based polymers have a high proportion of aromatic structures in the main chain and belong to the class of thermally stable polymers. Such polymers contain structures that impart high melting temperatures, resistance to oxidative degradation and stability to radiation and chemical reagents. Among the thermally stable polymers with commercial relevance are polyimides, polysulfones, polyetherketones, and polybenzimidazoles. Of these, polyimides are most widely applied.[15] The polymers’ structures result also in poor processing characteristics, in particular a high melting point and low solubility. The named properties are in particular based on a high percentage of aromatic carbons in the polymer backbone which produces a certain stiffness.[16] Approaches for an improvement of processability include the incorporation of flexible spacers into the backbone, the attachment of stable pendent groups or the incorporation of non-symmetrical structures.[15] Flexible spacers include, for example, ether or hexafluoroisopropylidene, carbonyl or aliphatic groups like isopropylidene; these groups allow bond rotation between aromatic rings. Less symmetrical structures, for example based on meta- or ortho-linked monomers introduce structural disorder and thereby decrease the crystallinity.[7]
The generally poor processability of aromatic polymers (for example, a high melting point and a low solubility) also limits the available options for synthesis and may require strong electron-donating co-solvents like HFIP or TFA for analysis (e. g. 1H NMR spectroscopy) which themselves can introduce further practical limitations.
Uses and applications[edit]
Fabrics woven or knitted from polyester thread or yarn are used extensively in apparel and home furnishings, from shirts and pants to jackets and hats, bed sheets, blankets, upholstered furniture and computer mouse mats. Industrial polyester fibers, yarns and ropes are used in car tire reinforcements, fabrics for conveyor belts, safety belts, coated fabrics and plastic reinforcements with high-energy absorption. Polyester fiber is used as cushioning and insulating material in pillows, comforters and upholstery padding. Polyester fabrics are highly stain-resistant—in fact, the only class of dyes which can be used to alter the color of polyester fabric are what are known as disperse dyes.[17]
Polyesters are also used to make bottles, films, tarpaulin, sails (Dacron), canoes, liquid crystal displays, holograms, filters, dielectric film for capacitors, film insulation for wire and insulating tapes. Polyesters are widely used as a finish on high-quality wood products such as guitars, pianos and vehicle/yacht interiors. Thixotropic properties of spray-applicable polyesters make them ideal for use on open-grain timbers, as they can quickly fill wood grain, with a high-build film thickness per coat. Cured polyesters can be sanded and polished to a high-gloss, durable finish.
Industry[edit]
Basics[edit]
Polyethylene terephthalate, the polyester with the greatest market share, is a synthetic polymer made of purified terephthalic acid (PTA) or its dimethyl ester dimethyl terephthalate (DMT) and monoethylene glycol (MEG). With 18% market share of all plastic materials produced, it ranges third after polyethylene (33.5%) and polypropylene (19.5%) and is counted as commodity plastic.
There are several reasons for the importance of polyethylene terephthalate:
The relatively easy accessible raw materials PTA or DMT and MEG
The very well understood and described simple chemical process of its synthesis
The low toxicity level of all raw materials and side products during production and processing
The possibility to produce PET in a closed loop at low emissions to the environment
The outstanding mechanical and chemical properties
The recyclability
The wide variety of intermediate and final products.
In the following table, the estimated world polyester production is shown. Main applications are textile polyester, bottle polyester resin, film polyester mainly for packaging and specialty polyesters for engineering plastics. According to this table, the world’s total polyester production might exceed 50 million tons per annum before the year 2010.
World polyester production by year
Product type 2002 (million tonnes/year) 2008 (million tonnes/year)
Textile-PET 20 39
Resin, bottle/A-PET 9 16
Film-PET 1.2 1.5
Special polyester 1 2.5
Total 31.2 59
Polyester processing[edit]
After the first stage of polymer production in the melt phase, the product stream divides into two different application areas which are mainly textile applications and packaging applications. In the following table, the main applications of textile and packaging of polyester are listed.
Textile and packaging polyester application list (melt or pellet)
Textile Packaging
Staple fiber (PSF) Bottles for CSD, water, beer, juice, detergents, etc.
Filaments POY, DTY, FDY A-PET film
Technical yarn and tire cord Thermoforming
Non-woven and spunbond biaxial-oriented film (BO-PET)
Mono-filament Strapping
Abbreviations:
PSF
Polyester-staple fiber;
POY
Partially oriented yarn;
DTY
Drawn textured yarn;
FDY
Fully drawn yarn;
CSD
Carbonated soft drink;
A-PET
Amorphous polyethylene terephthalate film;
BO-PET
Biaxial-oriented polyethylene terephthalate film;
A comparable small market segment (much less than 1 million tonnes/year) of polyester is used to produce engineering plastics and masterbatch.
In order to produce the polyester melt with a high efficiency, high-output processing steps like staple fiber (50–300 tonnes/day per spinning line) or POY /FDY (up to 600 tonnes/day split into about 10 spinning machines) are meanwhile more and more vertically integrated direct processes. This means the polymer melt is directly converted into the textile fibers or filaments without the common step of pelletizing. We are talking about full vertical integration when polyester is produced at one site starting from crude oil or distillation products in the chain oil → benzene → PX → PTA → PET melt → fiber/filament or bottle-grade resin. Such integrated processes are meanwhile established in more or less interrupted processes at one production site. Eastman Chemicals were the first to introduce the idea of closing the chain from PX to PET resin with their so-called INTEGREX process. The capacity of such vertically integrated production sites is >1000 tonnes/day and can easily reach 2500 tonnes/day.
Besides the above-mentioned large processing units to produce staple fiber or yarns, there are ten thousands of small and very small processing plants, so that one can estimate that polyester is processed and recycled in more than 10 000 plants around the globe. This is without counting all the companies involved in the supply industry, beginning with engineering and processing machines and ending with special additives, stabilizers and colors. This is a gigantic industry complex and it is still growing by 4–8% per year, depending on the world region.
Synthesis[edit]
Synthesis of polyesters is generally achieved by a polycondensation reaction. See “condensation reactions in polymer chemistry”. The general equation for the reaction of a diol with a diacid is :
(n+1) R(OH)2 + n R´(COOH)2 → HO[ROOCR´COO]nROH + 2n H2O.
Polyesters can be obtained by a wide range of reactions of which the most important are the reaction of acids and alcohols, alcoholysis and or acidolysis of low-molecular weight esters or the alcoholysis of acyl chlorides. The following figure gives an overview over such typical polycondensation reactions for polyester production. Furthermore, polyesters are accessible via ring-opening polymerization.
Overview polyester formation reaction.svg
Azeotrope esterification[edit]
In this classical method, an alcohol and a carboxylic acid react to form a carboxylic ester. To assemble a polymer, the water formed by the reaction must be continually removed by azeotrope distillation.
Melt esterification[edit]
When melting points of the monomers are sufficiently low, a polyester can be formed via direct esterification while removing the reaction water via vacuum.
Polyester formation via direct esterification.svg
Direct bulk polyesterification at high temperatures (150 – 290 °C) is well-suited and used on the industrial scale for the production of aliphatic polyesters, unsaturated polyesters and aromatic–aliphatic polyesters. Monomers containing phenolic or tertiary hydroxyl groups exhibit a low reactivity with carboxylic acids and cannot be polymerized via direct acid alcohol-based polyesterification.[7] In the case of PET production, however, the direct process has several advantages, in particular a higher reaction rate, a higher attainable molecular weight, the release of water instead of methanol and lower storage costs of the acid when compared to the ester due to the lower weight.[1]
Alcoholic transesterification[edit]
Polyester formation via transesterification.svg
Transesterification: An alcohol-terminated oligomer and an ester-terminated oligomer condense to form an ester linkage, with loss of an alcohol. R and R’ are the two oligomer chains, R” is a sacrificial unit such as a methyl group (methanol is the byproduct of the esterification reaction).
The term transesterification is typically used to describe hydroxy–ester, carboxy–ester, and ester–ester exchange reactions. The hydroxy–ester exchange reaction possesses the highest rate of reaction and is used for the production of numerous aromatic–aliphatic and wholly aromatic polyesters.[7] The transesterification based synthesis is particularly useful for when high melting and poorly soluble dicarboxylic acids are used. In addition, alcohols as condensation product are more volatile and thereby easier to remove than water.[18]
The high-temperature melt synthesis between bisphenol diacetates and aromatic dicarboxylic acids or in reverse between bisphenols and aromatic dicarboxylic acid diphenyl esters (carried out at 220 to 320 °C upon the release of acetic acid) is, besides the acyl chloride based synthesis, the preferred route to wholly aromatic polyesters.[7]
Acylation[edit]
In acylation, the acid begins as an acid chloride, and thus the polycondensation proceeds with emission of hydrochloric acid (HCl) instead of water.
The reaction between diacyl chlorides and alcohols or phenolic compounds has been widely applied to polyester synthesis and has been subject of numerous reviews and book chapters.[7][19][20][21] The reaction is carried out at lower temperatures than the equilibrium methods; possible types are the high-temperature solution condensation, amine catalysed and interfacial reactions. In addition, the use of activating agents is counted as non-equilibrium method. The equilibrium constants for the acyl chloride-based condensation yielding yielding arylates and polyarylates are very high indeed and are reported to be 4.3 × 103 and 4.7 × 103, respectively. This reaction is thus often referred to as a ‘non-equilibrium’ polyesterification. Even though the acyl chloride based synthesis is also subject of reports in the patent literature, it is unlikely that the reaction is utilized on the production scale.[22] The method is limited by the acid dichlorides’ high cost, its sensitivity to hydrolysis and the occurrence of side reactions.[23]
The high temperature reaction (100 to > 300 °C) of an diacyl chloride with an dialcohol yields the polyester and hydrogen chloride. Under these relatively high temperatures the reaction proceeds rapidly without a catalyst:[21]
Polyester formation via neat acyl chloride.svg
The conversion of the reaction can be followed by titration of the evolved hydrogen chloride. A wide variety of solvents has been described including chlorinated benzenes (e.g. dichlorobenzene), chlorinated naphthalenes or diphenyls, as well as non-chlorinated aromatics like terphenyls, benzophenones or dibenzylbenzenes. The reaction was also applied successfully to the preparation of highly crystalline and poorly soluble polymers which require high temperatures to be kept in solution (at least until a sufficiently high molecular weight was achieved).[24]
In an interfacial acyl chloride-based reaction, the alcohol (generally in fact a phenol) is dissolved in the form of an alkoxide in an aqueous sodium hydroxide solution, the acyl chloride in an organic solvent immiscible with water such as dichloromethane, chlorobenzene or hexane, the reaction occurs at the interface under high-speed agitation near room temperature.[21]
Polyester formation via interfacial acyl chloride.svg
The procedure is used for the production of polyarylates (polyesters based on bisphenols), polyamides, polycarbonates, poly(thiocarbonate)s, and others. Since the molecular weight of the product obtained by a high-temperature synthesis can be seriously limited by side reactions, this problem is circumvented by the mild temperatures of interfacial polycondensation. The procedure is applied to the commercial production of bisphenol-A-based polyarylates like Unitika’s U-Polymer.[7] Water could be in some cases replaced by an immiscible organic solvent (e. g. in the adiponitrile/carbon tetrachloride system).[21] The procedure is of little use in the production of polyesters based on aliphatic diols which have higher pKa values than phenols and therefore do not form alcoholate ions in aqueous solutions.[7] The base catalysed reaction of an acyl chloride with an alcohol may also be carried out in one phase using tertiary amines (e. g. triethylamine, Et3N) or pyridine as acid acceptors:
Polyester formation via amine acyl chloride.svg
While acyl chloride-based polyesterifications proceed only very slowly at room temperature without a catalyst, the amine accelerates the reaction in several possible ways, although the mechanism is not fully understood.[21] However, it is known that tertiary amines can cause side-reactions such as the formation of ketenes and ketene dimers.[25]
Silyl method
In this variant of the HCl method, the carboxylic acid chloride is converted with the trimethyl silyl ether of the alcohol component and production of trimethyl silyl chloride is obtained
Acetate method (esterification)[edit]
Polyester formation via transesterification.svg
Silyl acetate method
Ring-opening polymerization[edit]
Polyester ring-opening formation.svg
Aliphatic polyesters can be assembled from lactones under very mild conditions, catalyzed anionically, cationically, metallorganically or enzyme-based[26][27] A number of catalytic methods for the copolymerization of epoxides with cyclic anhydrides have also recently been shown to provide a wide array of functionalized polyesters, both saturated and unsaturated. Ring-opening polymerization of lactones and lactides is also applied on the industrial scale.[28][29]
Other methods[edit]
Numerous other reactions have been reported for the synthesis of selected polyesters, but are limited to laboratory-scale syntheses using specific conditions, for example using dicarboxylic acid salts and dialkyl halides or reactions between bisketenes and diols.[7]
Instead of acyl chlorides, so-called activating agents can be used, such as 1,1′-carbonyldiimidazole, dicyclohexylcarbodiimide, or trifluoroacetic anhydride. The polycondensation proceeds via the in situ conversion of the carboxylic acid into a more reactive intermediate while the activating agents are consumed. The reaction proceeds, for example, via an intermediate N-acylimidazole which reacts with catalytically acting sodium alkoxide:[7]
Polyester formation via reactive reagent.svg
The use of activating agents for the production of high-melting aromatic polyesters and polyamides under mild conditions has been subject of intensive academic research since the 1980s, but the reactions have not gained commercial acceptance as similar results can be achieved with cheaper reactants.[7]
Thermodynamics of polycondensation reactions[edit]
Polyesterifications are grouped by some authors[7][19] into two main categories: a) equilibrium polyesterifications (mainly alcohol-acid reaction, alcohol–ester and acid–ester interchange reactions, carried out in bulk at high temperatures), and b) non-equilibrium polyesterifications, using highly reactive monomers (for example acid chlorides or activated carboxylic acids, mostly carried out at lower temperatures in solution).
The acid-alcohol based polyesterification is one example of an equilibrium reaction. The ratio between the polymer-forming ester group (-C(O)O-) and the condensation product water (H2O) against the acid-based (-C(O)OH) and alcohol-based (-OH) monomers is described by the equilibrium constant KC.
{\displaystyle K_{C}={\frac {[…-C(O)O-…][H_{2}O]}{[-C(O)OH][-OH]}}}
The equilibrium constant of the acid-alcohol based polyesterification is typically KC ≤ 10, what is not high enough to obtain high-molecular weight polymers (DPn ≥ 100), as the number average degree of polymerization (DPn) can be calculated from the equilibrium constant KC.[20]
{\displaystyle DP_{n}~=~{\sqrt[{2}]{K_{C}}}+1}
In equilibrium reactions, it is therefore necessary to remove the condensation product continuously and efficiently from the reaction medium in order to drive the equilibrium towards polymer.[20] The condensation product is therefore removed at reduced pressure and high temperatures (150–320 °C, depending on the monomers) to prevent the back reaction.[9] With the progress of the reaction, the concentration of active chain ends is decreasing and the viscosity of the melt or solution increasing. For an increase of the reaction rate, the reaction is carried out at high end group concentration (preferably in the bulk), promoted by the elevated temperatures.
Equilibrium constants of magnitude KC ≥ 104 are achieved when using reactive reactants (acid chlorides or acid anhydrides) or activating agents like 1,1′-carbonyldiimidazole. Using these reactants, molecular weights required for technical applications can be achieved even without active removal of the condensation product.
History[edit]
In 1926, United States-based E.I. du Pont de Nemours and Co. began research on large molecules and synthetic fibers. This early research, headed by W.H. Carothers, centered on what became nylon, which was one of the first synthetic fibers.[30] Carothers was working for duPont at the time. Carother’s research was incomplete and had not advanced to investigating the polyester formed from mixing ethylene glycol and terephthalic acid. In 1928 polyester was patented in Britain by the International General Electric company.[31] Carothers’ project was revived by British scientists Whinfield and Dickson, who patented polyethylene terephthalate (PET) or PETE in 1941. Polyethylene terephthalate forms the basis for synthetic fibers like Dacron, Terylene and polyester. In 1946, duPont bought all legal rights from Imperial Chemical Industries (ICI).[32]
Biodegradation and environmental concerns[edit]
The futuro house was made of fibreglass-reinforced polyester plastic; polyester-polyurethane, and poly(methylmethacrylate) one of them was found to be degrading by Cyanobacteria and Archaea.[33][34]
Cross-linking[edit]
Unsaturated polyesters are thermosetting resins. They are generally copolymers prepared by polymerizing one or more diol with saturated and unsaturated dicarboxylic acids (maleic acid, fumaric acid…) or their anhydrides. The double bond of unsaturated polyesters reacts with a vinyl monomer, usually styrene, resulting in a 3-D cross-linked structure. This structure acts as a thermoset. The exothermic cross-linking reaction is initiated through a catalyst, usually an organic peroxide such as methyl ethyl ketone peroxide or benzoyl peroxide.
Pollution of freshwater and seawater habitats[edit]
A team at Plymouth University in the UK spent 12 months analysing what happened when a number of synthetic materials were washed at different temperatures in domestic washing machines, using different combinations of detergents, to quantify the microfibres shed. They found that an average washing load of 6 kg could release an estimated 137,951 fibres from polyester-cotton blend fabric, 496,030 fibres from polyester and 728,789 from acrylic. Those fibers add to the general microplastics pollution.[35][36][37]
Non-renewable[edit]
Polyester is a synthetic petroleum-based fibre, and is therefore a non-renewable carbon-intensive resource.[38] Nearly 70 million barrels of oil are used each year to make polyester around the world, which is now the most commonly used fiber in making clothes. But it takes more than 200 years to decompose.[39]
See also[edit]
Denim
Glycerine phthalate
Microfiber
Oligoester
Polyamide
Rayon
Viscose
References[edit]
^ Jump up to: a b c d Köpnick H, Schmidt M, Brügging W, Rüter J, Kaminsky W (June 2000). “Polyesters”. Ullmann’s Encyclopedia of Industrial Chemistry. Weinheim, Germany: Wiley-VCH Verlag GmbH & Co. KGaA.
^ Mendelson C (17 May 2005). Home Comforts: The Art and Science of Keeping House. Simon and Schuster. ISBN 9780743272865.
^ “Thermal Spray Abradable Coatings”. www.gordonengland.co.uk. Retrieved 12 December 2018.
^ Chandru K, Mamajanov I, Cleaves HJ, Jia TZ (January 2020). “Polyesters as a Model System for Building Primitive Biologies from Non-Biological Prebiotic Chemistry”. Life. 10 (1): 6. doi:10.3390/life10010006. PMC 7175156. PMID 31963928.
^ Jia TZ, Chandru K, Hongo Y, Afrin R, Usui T, Myojo K, Cleaves HJ (August 2019). “Membraneless polyester microdroplets as primordial compartments at the origins of life”. Proceedings of the National Academy of Sciences of the United States of America. 116 (32): 15830–15835. doi:10.1073/pnas.1902336116. PMC 6690027. PMID 31332006.
^ Chandru K, Guttenberg N, Giri C, Hongo Y, Butch C, Mamajanov I, Cleaves HJ (31 May 2018). “Simple prebiotic synthesis of high diversity dynamic combinatorial polyester libraries”. Communications Chemistry. 1 (1). doi:10.1038/s42004-018-0031-1.
^ Jump up to: a b c d e f g h i j k l Rogers ME, Long TE (2003). Synthetic Methods in Step-Growth Polymers. Hoboken, NJ, USA: John Wiley & Sons, Inc.
^ Kong X, Qi H, Curtis JM (August 2014). “Synthesis and characterization of high‐molecular weight aliphatic polyesters from monomers derived from renewable resources”. Journal of Applied Polymer Science. 131 (15): 40579–40586. doi:10.1002/app.40579.
^ Jump up to: a b Park HS, Seo JA, Lee HY, Kim HW, Wall IB, Gong MS, Knowles JC (August 2012). “Synthesis of elastic biodegradable polyesters of ethylene glycol and butylene glycol from sebacic acid”. Acta Biomaterialia. 8 (8): 2911–8. doi:10.1016/j.actbio.2012.04.026. PMID 22522011.
^ Gurunathan T, Mohanty S, Nayak SK (January 2016). “Hyperbranched polymers for coating applications: a review”. Polymer-Plastics Technology and Engineering. 55 (1): 92–117. doi:10.1080/03602559.2015.1021482. S2CID 100936296.
^ Testud B, Pintori D, Grau E, Taton D, Cramail H (2017). “Hyperbranched polyesters by polycondensation of fatty acid-based AB n-type monomers”. Green Chemistry. 19 (1): 259–69. arXiv:1911.07737. doi:10.1039/C6GC02294D. S2CID 102450135.
^ Rosato DV, Rosato DV, Rosato MV (2004). Plastic product material and process selection handbook. Elsevier. p. 85. ISBN 978-1-85617-431-2.
^ Parker, David; Bussink, Jan; van de Grampel, Hendrik T.; Wheatley, Gary W.; Dorf, Ernst-Ulrich; Ostlinning, Edgar; Reinking, Klaus; Schubert, Frank; Jünger, Oliver (15 April 2012), Wiley-VCH Verlag GmbH & Co. KGaA (ed.), “Polymers, High-Temperature”, Ullmann’s Encyclopedia of Industrial Chemistry, Weinheim, Germany: Wiley-VCH Verlag GmbH & Co. KGaA, pp. a21_449.pub3, doi:10.1002/14356007.a21_449.pub4, ISBN 978-3-527-30673-2, retrieved 13 December 2020
^ H.-G. Elias and R. Mülhaupt, in Ullmann’s Encyclopedia of Industrial Chemistry, Wiley-VCH Verlag GmbH & Co. KGaA, Weinheim, Germany, 2015, pp. 1–70.
^ Jump up to: a b P. E. Cassidy, T. M. Aminabhavi and V. S. Reddy, in Kirk-Othmer Encyclopedia of Chemical Technology, John Wiley & Sons, Inc., Hoboken, NJ, USA, 2000.
^ T. Whelan, Polymer Technology Dictionary, Springer Netherlands, Dordrecht, 1994.
^ Schuler MJ (1981). “Part 8: Dyeing with disperse dyes”. Dyeing Primer. AATCC. p. 21. GGKEY:SK3T00EYAFR.
^ Ravve A (2012). Principles of Polymer Chemistry. New York, New York, NY: Springer.
^ Jump up to: a b Vinogradova SV (January 1977). “The basic principles of non-equilibrium polycondensation”. Polymer Science USSR. 19 (4): 769–808. doi:10.1016/0032-3950(77)90232-5.
^ Jump up to: a b c Duda A, Penczek S (2005). “Mechanisms of Aliphatic Polyester Formation”. In Doi Y, Steinbüchel A (eds.). Biopolymers Online. Weinheim, Germany: Wiley-VCH Verlag GmbH & Co. KGaA. pp. 371–383. doi:10.1002/3527600035.bpol3b12.
^ Jump up to: a b c d e Pilati F (1989). “Polyesters”. Comprehensive Polymer Science and Supplements. 5. Elsevier. pp. 275–315.
^ Lienert KW (1999). “Poly (ester-imide)s for industrial use.”. In Kricheldorf HR (ed.). Progress in Polyimide Chemistry II. Advances in Polymer Science. 141. Berlin, Heidelberg: Springer. pp. 45–82. doi:10.1007/3-540-49814-1_2. ISBN 978-3-540-64963-2.
^ Sokolsky-Papkov M, Langer R, Domb AJ (April 2011). “Synthesis of aliphatic polyesters by polycondensation using inorganic acid as catalyst”. Polymers for Advanced Technologies. 22 (5): 502–511. doi:10.1002/pat.1541. PMC 4249767. PMID 25473252.
^ Sokolsky-Papkov M, Langer R, Domb AJ (April 2011). “Synthesis of aliphatic polyesters by polycondensation using inorganic acid as catalyst”. Polymers for Advanced Technologies. 22 (5): 502–511. doi:10.1002/pat.1541. PMC 4249767. PMID 25473252.
^ Kricheldorf HR, Nuyken O, Swift G (2004). Handbook of Polyermer Synthesis (2nd ed.). CRC Press. ISBN 0-367-57822-0. OCLC 1156408945.
^ Varma IK, Albertsson AC, Rajkhowa R, Srivastava RK (October 2005). “Enzyme catalyzed synthesis of polyesters”. Progress in Polymer Science. 30 (10): 949–81. doi:10.1016/j.progpolymsci.2005.06.010.
^ Nuyken O, Pask SD (April 2013). “Ring-Opening Polymerization—An Introductory Review”. Polymers. 5 (2): 361–403. doi:10.3390/polym5020361. ISSN 2073-4360.
^ Jérôme C, Lecomte P (June 2008). “Recent advances in the synthesis of aliphatic polyesters by ring-opening polymerization”. Advanced Drug Delivery Reviews. 60 (9): 1056–76. doi:10.1016/j.addr.2008.02.008. PMID 18403043.
^ Dechy-Cabaret O, Martin-Vaca B, Bourissou D (December 2004). “Controlled ring-opening polymerization of lactide and glycolide”. Chemical Reviews. 104 (12): 6147–76. doi:10.1021/cr040002s. PMID 15584698.
^ “How polyester is made – material, manufacture, making, history, used, structure, steps, product, History”. www.madehow.com. Retrieved 4 December 2018.
^ Loasby G (1951). “The Development of the Synthetic Fibres”. Journal of the Textile Institute Proceedings. 42 (8): P411–P441. doi:10.1080/19447015108663852.
^ “History of Polyester | What is Polyester”. www.whatispolyester.com. Retrieved 4 December 2018.
^ Cappitelli F, Principi P, Sorlini C (August 2006). “Biodeterioration of modern materials in contemporary collections: can biotechnology help?”. Trends in Biotechnology. 24 (8): 350–4. doi:10.1016/j.tibtech.2006.06.001. PMID 16782219.
^ Rinaldi A (November 2006). “Saving a fragile legacy. Biotechnology and microbiology are increasingly used to preserve and restore the world’s cultural heritage”. EMBO Reports. 7 (11): 1075–9. doi:10.1038/sj.embor.7400844. PMC 1679785. PMID 17077862.
^ O’Connor MC (27 October 2014). “Inside the lonely fight against the biggest environmental problem you’ve never heard of”. The Guardian.
^ Williams A. “Washing clothes releases thousands of microplastic particles into environment, study shows”. Plymouth University. Retrieved 9 October 2016.
^ Napper IE, Thompson RC (November 2016). “Release of synthetic microplastic plastic fibres from domestic washing machines: Effects of fabric type and washing conditions”. Marine Pollution Bulletin. 112 (1–2): 39–45. doi:10.1016/j.marpolbul.2016.09.025. hdl:10026.1/8163. PMID 27686821.
^ “The Environmental Impacts of Polyester”. tortoise & lady grey. 29 August 2016. Retrieved 12 December 2018.
^ Conca J. “Making Climate Change Fashionable – The Garment Industry Takes On Global Warming”. Forbes. Retrieved 12 December 2018.
Further reading[edit]
Textiles, by Sara Kadolph and Anna Langford. 8th Edition, 1998.
External links[edit]
Lipase catalyzed polyesterification: Enzyme-Catalyzed Polymerization of End-Functionalized Polymers in a Microreactor
en.wikipedia.org /wiki/Polyester
Polyester
Contributors to Wikimedia projects
31-39 minutes
Ester group (blue) which defines polyesters.
Close-up of a polyester shirt
SEM picture of a bend in a high-surface area polyester fiber with a seven-lobed cross section
.
.
.
.
.
.
.
.
.
.
.