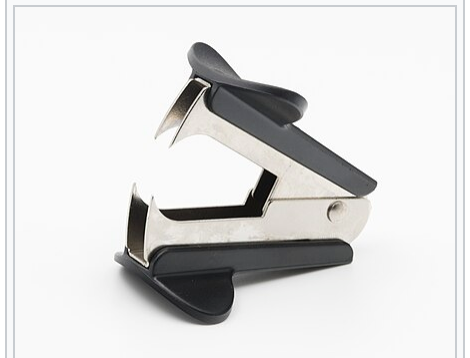
.
-as of [23 SEPTEMBER 2024]–
.
.
(also known as a de-stapler)
.
-a [staple remover] is a ‘device’ that allows for the quick removal of a ‘staple’ from a ‘material’ without causing [damage]-
.
The best-known form of staple remover, designed for light-gauge staples, consists of two opposing, pivot-mounted pairs of thin, steep wedges and a spring that returns the device to the open position after use
Although a simple metal wedge can be used for the same purpose, and although some staplers (especially small ones about 1.5 inches (3.8 cm) long) feature such a wedge at their hinge end, use of the wedge tends to tear fragile papers
.
Use
Proper use of the opposing wedge staple remover is debated
the two major methods are described below.
Original method[edit]
0:06
Demonstration of the “fast” removal method
The user clips the front flat side of the staple, forcing the folded tabs on the reverse side to open and pull through the entry holes.
Although this method is quick, it may tear the paper during removal.
The inventor of the original staple remover, William G. Pankonin, illustrates this method of removal in US Patent Number 2033050
.
“Safe” method
Incorrectly Using a staple remover
The following method reduces the risk of damage to the paper sheets being separated, albeit at some cost to speed and associated time efficiency:
Turn the paper over to the side of the paper (usually the back) over which the staple’s prongs have been folded.
Use each opposed pair of tines to clip one of the prongs, re-straightening them and in the process raising them from the paper.
Turn the paper back over to the front side against which the main body of the staple has been pressed.
Gently slide the tines on one side of the remover under the main body of the staple and press the remover’s halves together until you have a firm hold on the staple.
Continuing to maintain a firm hold on the staple, pull the entire staple gently out of the paper.
Proper for pen style remover:[1]
The metal tip should be placed just beneath the front side of the staple
Press the blade up and away from yourself to remove the staple from the papers
.
Design
A staple remover for carpentry staples
The design is focused on functionality and robustness with no unnecessary decoration (unless one includes the ergonomics of the handle) and minimised number of parts to lower costs and production time.
The device works with a pincer action to unfold and pull out a staple in one motion
.
Components
Blades[edit]
The two pivoting blades interlock each other. They are made of chrome-plated steel, which is harder than the thin ductile wire of the staple and strong enough to withstand the force required to remove it. The chrome plating provides a mild rust-resistance suitable for use in an office environment away from any liquids. Though the blade is made from what was originally sheet metal, the right angles and clean edges mean that a punch and die method of production would not be suitable. Therefore, the piece of sheet metal is cut using the process of blanking in a mechanical press, then bent in a press brake. This is a highly automated method which allows for a production rate of up to 1,500 units per minute.
Torsion springs[edit]
The torsion spring in this staple remover is a standardised component that appears in many other products, such as clothes pegs. It has two loops. The spring is made of chrome-plated steel, which is used because there is a point of minimum stress where continued use (opening and closing the staple remover) will not cause failure through fatigue. They are mass-produced by a spring winding machine which cold winds wire around an arbour before heat treating to make it harder. The spring is then chrome plated. The machinery to do this is large, expensive, but has a high production rate. That is why the springs are usually bought off-the-shelf from a tier 1 supplier rather than produced in house.
Plastic grips[edit]
The plastic grips are unnecessary and the device could still be operated without them. They provide enhanced ergonomics so the user does not have to press their fingers against sheet metal. Injection moulding of thermoplastics are normally used through the use of an automated injection moulding machine, which shoots liquid plastic into a mould where it is left to set. Such processing is commonplace, not very labour-intensive, cheap, and capable of producing high quantities. Plastic is used as it is the easiest, but also the cheapest and most readily available material that can be formed into such fluid shapes.
Pin axle[edit]
The pin axle provides a cylindrical bar from which the blades can rotate. It is made of stainless steel, which will not rust in areas that have been worn by contact with other metals. The process to create such a pin axle is quite intensive and hence it is bought off-the-shelf from a supplier. They are made by a specialised machine which cuts thick wire into a suitable length and then die punches the head of the pin. The supplier normally runs specialised machinery that is capable of producing large amounts of products at a high rate for a low cost.
History[edit]
While staplers had become available since late 1870s, first devices designed for removing staples have been patented in 1916.[2] The patents from the early 20th century have not made any impact on office toolware, mostly due to size and weight of then-standard staples.[2] The modern “magazine staple” became popular only after 1927.[3]
The today-recognized, clawed form of destapler was invented by William G. Pankonin of Chicago, Illinois. A patent application for the same was filed on 12 December 1932, granted on 3 March 1936 and published on 3 April 1936 as patent document US 2,033,050.[4] This patent was originally introduced to the market by Ace Fastener Company as their Model No 600 Staple Remover, featuring patent number engraved on the side. It was available in 1935, and the first known advertisement for No 600 comes from 1937.[2] The model was slightly redesigned in approx. 1948, and around 1950 steel handles have been replaced with plastic ones.[2] Ace stopped producing No 600 after being acquired by another company in the 1990s, but other companies kept producing staple removers very similar to No 600.[2]
A modified version, also capable of removing broken staples, was patented by Joseph A. Foitle of Overland Park, Kansas, but does not see widespread use, despite overcoming several disadvantages of the former device by a simple, yet novel and inventive, modification. The patent for the latter invention was filed on 28 May 1969 and was granted on 28 December 1971, published as US 3,630,486 A. An excerpt from the patent application reads as follows:
… A device for removing broken portions of wire staples … comprising a pair of overlying planar arms pivoted together on an axis normal thereto, said arms having cooperating notches … whereby relative pivotal motions … may be engaged over the projecting portion of a broken staple…
See also[edit]
Staple knocker
Staple gun
References[edit]
^ “How to Use a Staple Remover”. Bostitch Office.
^ Jump up to: a b c d e Parsons, Frank (2020-05-11). “Ace Model 600 Staple Remover”. American Stationer. Retrieved 2022-03-14.
^ “Staplers, Paper Fasteners, Paper Clips”. www.officemuseum.com. Retrieved 2022-03-14.
^ US2033050A, Pankonin, William G., “Tool for removing staples”, issued 1936-03-03
External links[edit]
Media related to Staple removers at Wikimedia Commons
en.wikipedia.org /wiki/Staple_remover
Staple remover
Contributors to Wikimedia projects7-9 minutes 2/7/2005
From Wikipedia, the free encyclopedia
Staple remover
.
.
.
.
.
.
.
.
.
.
.